The crafting process (part 2)
As demonstrated in the initial phase of crafting this illuminated stainless steel world map, our process started with cutting the base layer from a corten steel plate using our fiber laser. Subsequently, our steel supplier prepared the stainless steel for cutting. Once the top layer was cut and engraved, we proceeded to work on the middle layer composed of acrylic, which houses the LED lights.
Finalising the stainless steel
Following the completion of cutting all stainless steel components, we carefully remove them from the steel plate and machine bed. After a thorough inspection, each piece is dismantled and subjected to a degreasing process. Removal of grease from the surface is essential before manually extracting the smaller islands, which remain attached to the steel plate due to residual connections from the cutting process. The machine parameters were intentionally set to prevent these smaller parts from falling through the machine bed into the collection container, reducing the risk of damage to the steel.
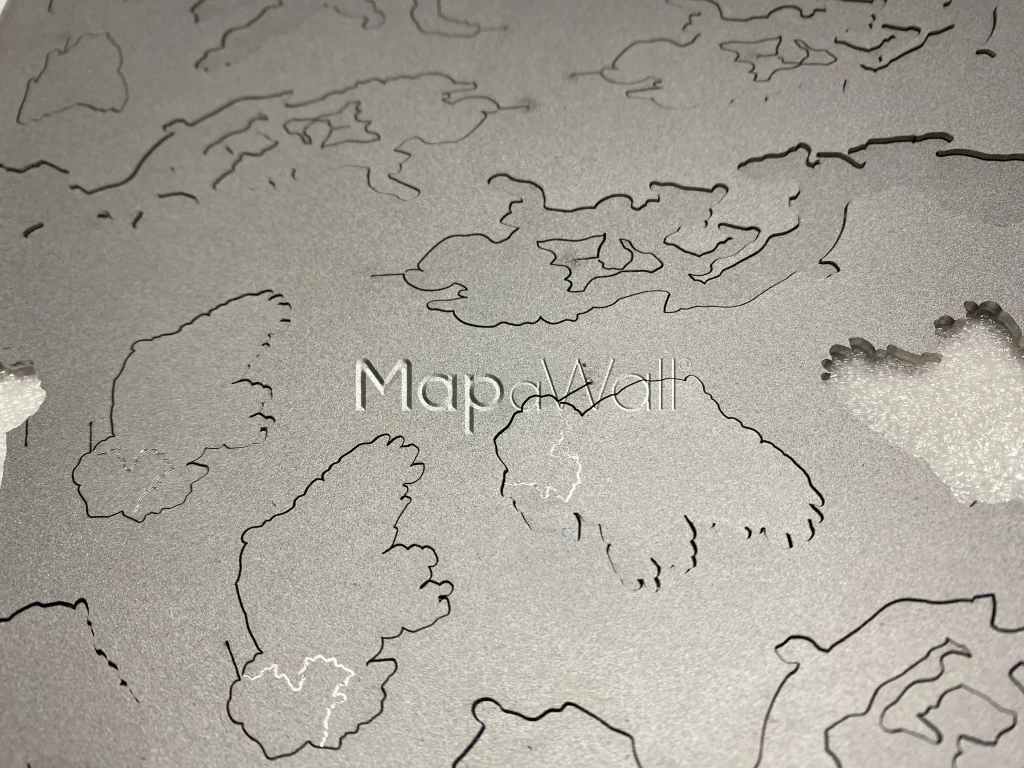
Once all components are set aside and degreased, a brief polishing session will take place that gives the surface an extra shine. This not only adds a dazzling finish to the stainless steel but also allows us to identify any unforeseen damages or scratches. In the event of such imperfections, the fiber laser will cut replacement pieces as necessary.
Crafting the acrylic layer for the LED lights
When we start with the fabrication of the acrylic layer that is positioned in the middle of the two metal layers, we start using our CO2 laser. This laser's frequency enables a sharper cut, rendering it more suitable for this task compared to the fiber laser. After configuring all parameters, the acrylic plate is carefully positioned on the machine bed. Next, the CO2 laser not only cuts the contours of the complete world map and its components but also carves out a space with an offset from the side for the eventual placement of the LED-strip. This cutting process demands considerable time as the laser traverses nearly three times the contour distance. Upon completion, the inner and outer pieces must be delicately removed from the machine bed, given the fragility of acrylic which may break if unsupported, especially the outer parts.
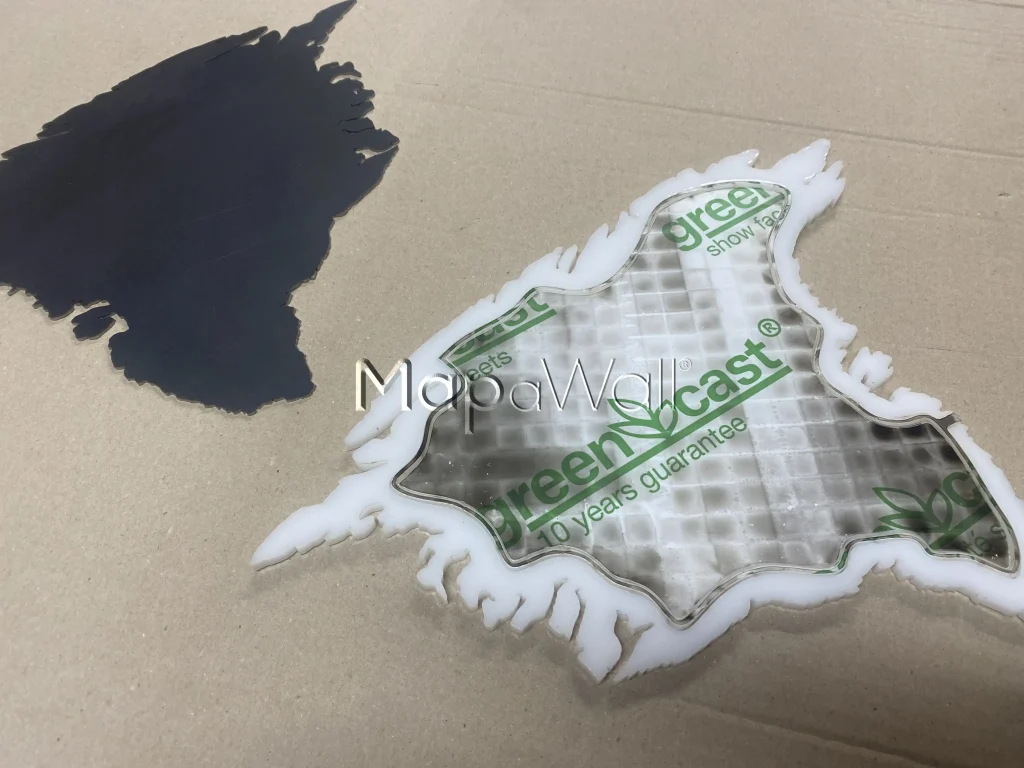
Glueing the corten steel to the acrylic
Following the cutting of all acrylic continents and islands, the protective foil is manually peeled off. Each acrylic piece is then fixed to its steel counterpart using a special glue suitable for both acrylic and steel. Precision is key in this stage as there's no room for error; the two parts must align perfectly upon initial contact since the special glue sets immediately. Additionally, careful application of the glue to both surfaces is crucial, ensuring no excess glue remains in areas where the slots will be removed. Any adhesive residue in these areas would complicate the extraction of acrylic cutouts intended for housing the LED-strip. Once all parts are securely bonded and the cutouts are removed, the LED-strips can be inserted into the slots, as depicted in the accompanying photo.
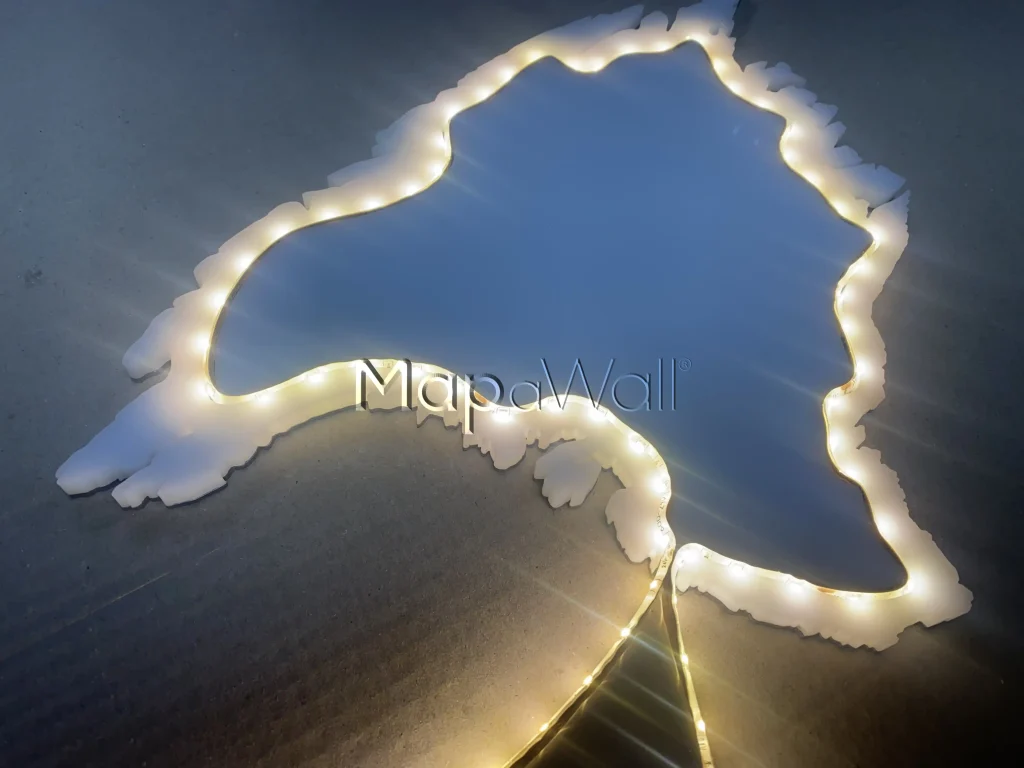
In our upcoming post next week, we will delve into the third and final phase of producing the illuminated stainless steel world maps. Stay tuned as we witness the assembly of all components into a unified, illuminated map and explore the measures taken to ensure its safe shipment worldwide.