The crafting process (part 3)
In our latest post, we discussed the initial phases of crafting the illuminated world map, including cutting the two layers of steel with our fiber laser and shaping the acrylic layer responsible for the diffusing light. We also showed how we integrated the LED string into the map, demonstrating the effectiveness of the diffused light through some photos.
Bringing together all components
Once the LED strings have been tested, all components are nearly ready to assemble into a three-layered map. However, before proceeding, we measure and weigh the larger stainless steel parts that will ultimately sit atop the acrylic layers, accounting for potential variations in weight and shape. Following this, we manually drill holes for the magnets that will secure the top layer in place. The photo below illustrates how the system will appear before the stainless steel is added.
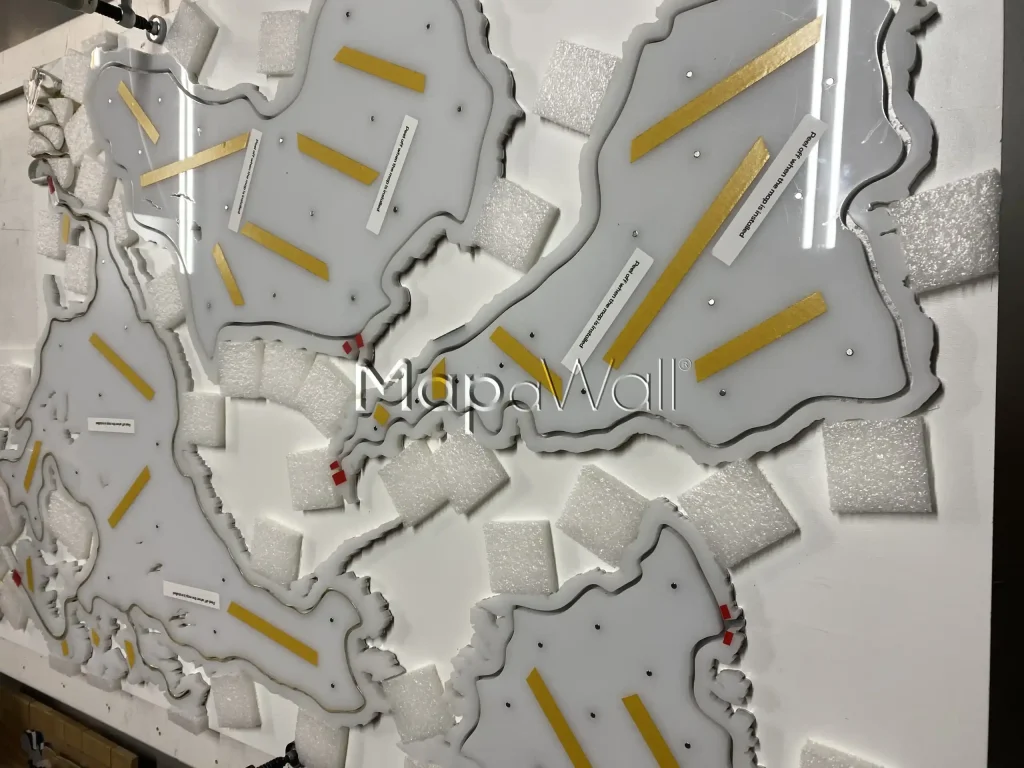
Ensuring safe transit
At MapaWall, our packing process is as crucial as the crafting of the maps itself. We take great care to secure the illuminated world map before shipment to any destination worldwide. Given that the illuminated world map includes two separate steel maps, each weighing approximately 20 kg (44 pounds), we pack each map in its own dedicated carton suitcase. To provide adequate support for these heavy components, we replace the standard carton inlays with lightweight wooden panels within the casing.
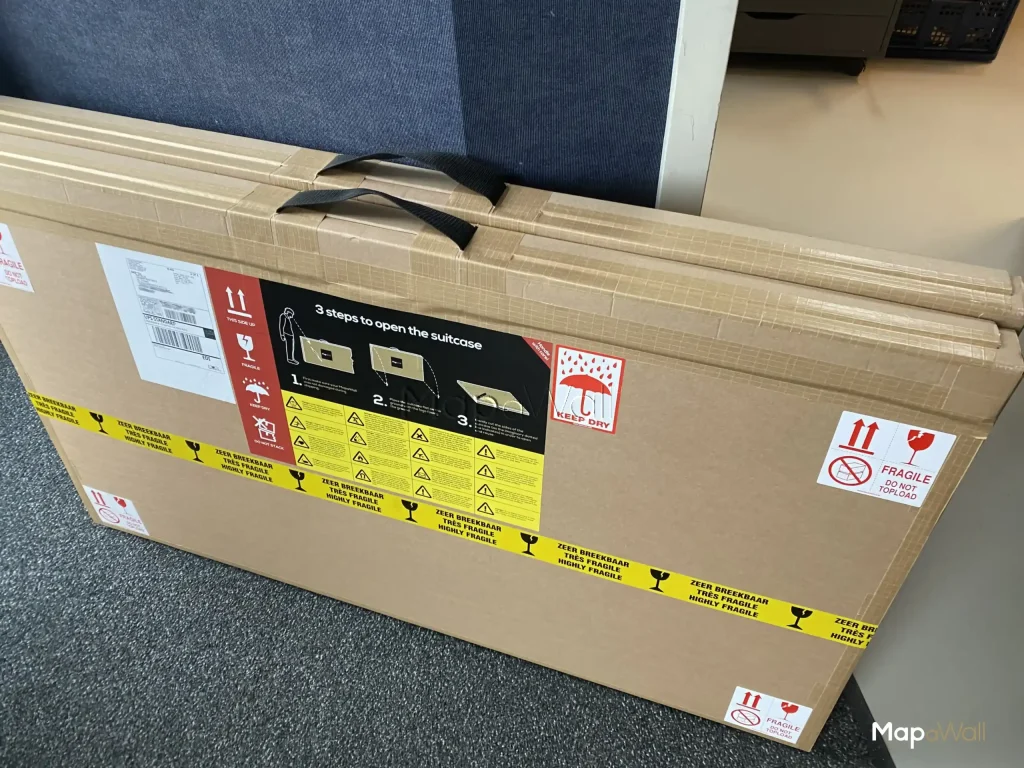
The photo above offers a glimpse into how the illuminated maps are presented to the carrier, in our case, UPS Capital. While UPS Capital's services may come at a premium, we prioritise the safety and security of our valuable world maps during transit, ensuring they reach their destination without any damage.
We trust that this overview provides insight into the complexity and time-intensive nature of crafting an illuminated map, underscoring its value and worth before ordering an exclusive illuminated world map such as this one.
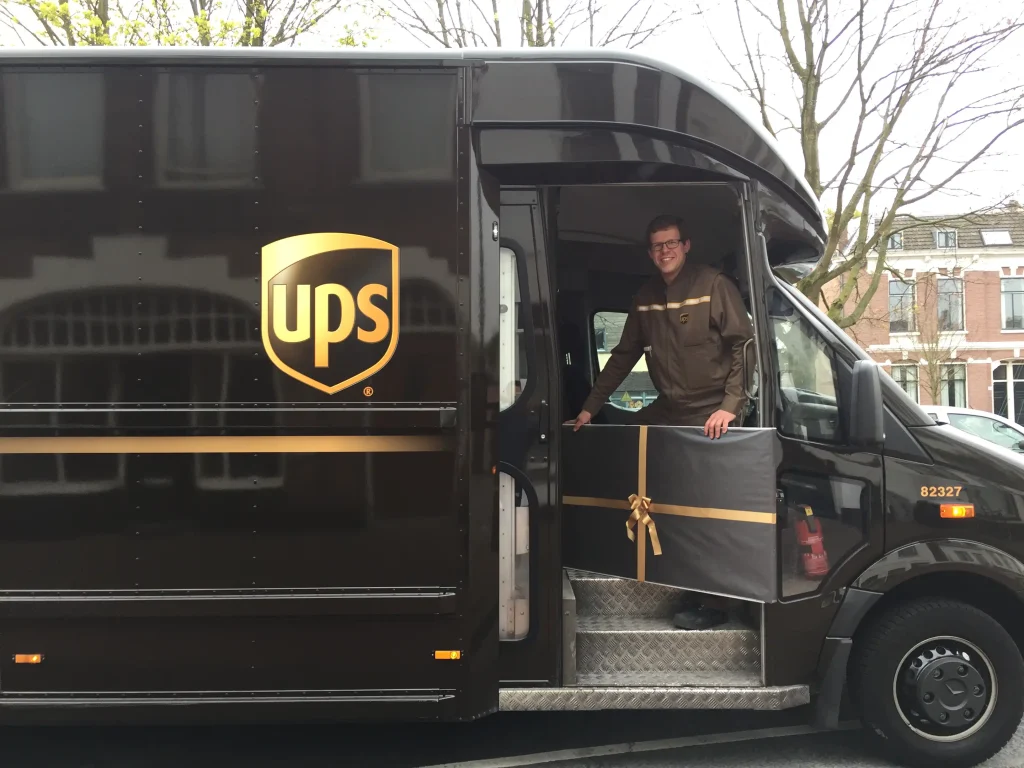